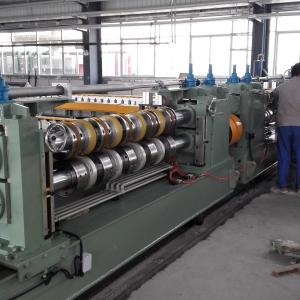
Add to Cart
Excellent aluminum coil coating line
aluminum foil rolls, centering machine, coated aluminium coil
Aluminium is a perfect substrate for colour coating, given its flat matt finish and high corrosion resistance. Aluminium consumption in the construction industry is growing, due to its weight differential compared to steel, making it suitable for long span roofing sheets, sandwich panels, composite panels and many other construction applications.
Methods of coating aluminium for construction applications are typically similar to that of steel, however, the sensitive surface, soft alloys, different micro structure and conductivity means some subtle differences must be considered when designing equipment for coating aluminium. The points below are aimed at highlighting these requirements.
Stitching / Slivers and Roll Cleaning
As with all continuous process lines it is necessary to join the aluminium coils. To do this a mechanical stitcher is used (see Figure 1), however, unlike steel, aluminium is prone to creating slivers during the stitching process. Air blowing systems can reduce these and the level of carryover. It is however preferable that roll cleaning is also included throughout the line to reduce any further carryover along the line. Scraper blades applied to each roll on the entry accumulator tower provides a significant reduction in line contamination, however, individual roll cleaners on the covered bridle rolls optimises line cleanliness and performance on highest quality coatings.Both of these items can be retrofitted to existing lines where cleanliness is an issue.
Process Flow
Main equipments according to processflow in turn are as follows:
Manually loading → entry skid → coil loading trolley I# & II# → pay off reel I# & II# → decoiling pinch rollI# & II# → transverse shearer I# & II# → join pinch roll → welder →riveter → roller leveler → tension bridle roll I# → entry accumulator → CPC double-roller centering machine I# → tension bridle roll II# → pre-degreasing →degreasing → washing I# → washing II# → purified water washing → hot air blowing device → chemical coating machine → chemical coating drying furnace →cold air blowing device → CPC double-roller centering machine II# → tension machine III# → base coating roller coater → base coating leveling chamber →base coating curing furnace → cold air blowing device → base coating forced cooling chamber → squeezing centering machine → hot air blowing device → tensionbridle roll IV# → CPC single roller centering machine I# → finishing coatingroller coater I# → finishing coating roller coater II# → leveling chamber → finishingcoating curing furnace → cold air blowing device → finishing coating forced cooling chamber → squeezing centering machine → hot air blowing device → tensionbridle roll V# → CPC double-roller centering machine III# → three color printing unit →printing thermal curing systemtensionbridle roll VI# → finishing roller coater → finishingleveling chamber → finishing curing furnace → hot laminating machine →finishing forced cooling chamber → squeezing centering machine → hot airblowing device → tension bridle roll VII# → cold laminating machine → exit accumulator→ CPC double-roller centering machine IV# → tension bridle roll VIII# → pinch shearer → exit pinch roll I# & II# → recoiler I# & II# (EPC) → coilunloading trolley I# & II# → auxiliary recoiler I# & II# → exit skid →manually unloading
Material | galvanized steel strip or common steel steel strip |
Line speed | whole line speed 40-150m/min |
End product weight | 3,500-15,000kg/coil |
Outer Dia. of coil | φ900-1,800mm |
Inner Dia. of coil | φ508/φ610mm |
Thickness of steel strip | 0.2-1.2mm |
Width of steel strip | 600-1,250mm |
Energy | produce gas/natural gas/blast furnace gas,steam and electricity |
Thickness of color plate | thickness of the frontsingle layer dry film can be adjusted between 10-20μm thickness of the reverse single layer dry film can beadjusted between 5-10μm |
Color plate quality | comply with the requirement ofnational standard GB/T12754-2006 |
Coiling staggered layer | one side≤1.0 mm |